Den kemiske sammensætning af keramisk sand er hovedsageligt Al2O3 og SiO2, og mineralfasen af keramisk sand er hovedsageligt korundfase og mullitfase samt en lille mængde amorf fase.Keramisk sands ildfasthed er generelt større end 1800°C, og det er et ildfast aluminium-siliciummateriale med høj hårdhed.
Karakteristika for keramisk sand
● Høj ildfasthed;
● Lille termisk udvidelseskoefficient;
● Høj varmeledningsevne;
● Omtrentlig sfærisk form, lille vinkelfaktor, god fluiditet og kompakt evne;
● Glat overflade, ingen revner, ingen ujævnheder;
● Neutralt materiale, velegnet til forskellige støbning af metalmaterialer;
● Partiklerne har høj styrke og brydes ikke let;
● Partikelstørrelsesområdet er bredt, og blandingen kan tilpasses efter proceskravene.
Påføring af keramisk sand i motorstøbegods
1. Brug keramisk sand til at løse åring, sandklæbning, brækket kerne og sandkernedeformation af støbejerns cylinderhoved
● Cylinderblok og topstykke er de vigtigste støbegods i motoren
● Formen af det indre hulrum er komplekst, og kravene til dimensionsnøjagtighed og indre hulrums renhed er høje
● Stort parti

For at sikre produktionseffektivitet og produktkvalitet,
● Grønt sand (hovedsagelig hydrostatisk stylinglinje) samlebåndsproduktion anvendes generelt.
● Sandkerner bruger generelt koldboks og harpiksbelagt sand (skalkerne) proces, og nogle sandkerner bruger hotbox-proces.
● På grund af den komplekse form af sandkernen af cylinderblokken og hovedstøbningen har nogle sandkerner et lille tværsnitsareal, den tyndeste del af nogle cylinderblokke og cylinderhovedvandkappekerner er kun 3-3,5 mm, og sandudløbet er smalt, sandkernen efter støbning omgivet af højtemperatursmeltet jern i lang tid, det er vanskeligt at rense sand, og der kræves specielt renseudstyr osv. Tidligere blev alt silicasand brugt til støbning produktion, hvilket gav åre- og sandklæbningsproblemer i vandkappestøbningen af cylinderblok og topstykke.Kernedeformation og knækkede kerneproblemer er meget almindelige og svære at løse.
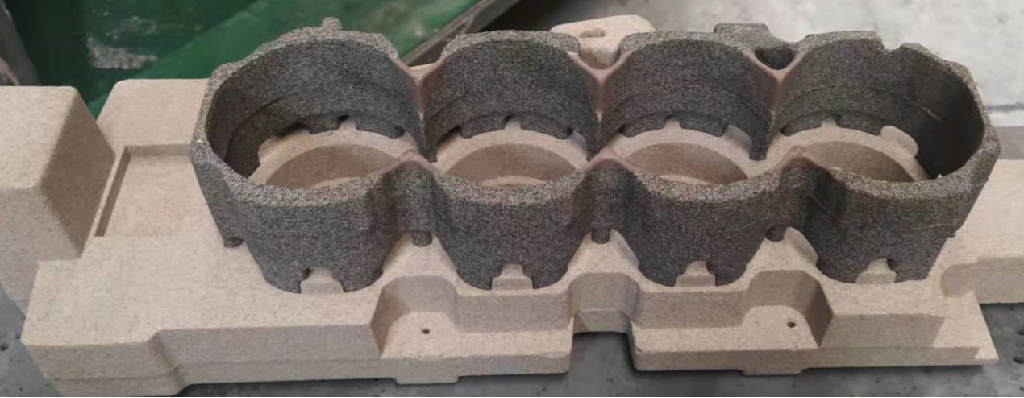
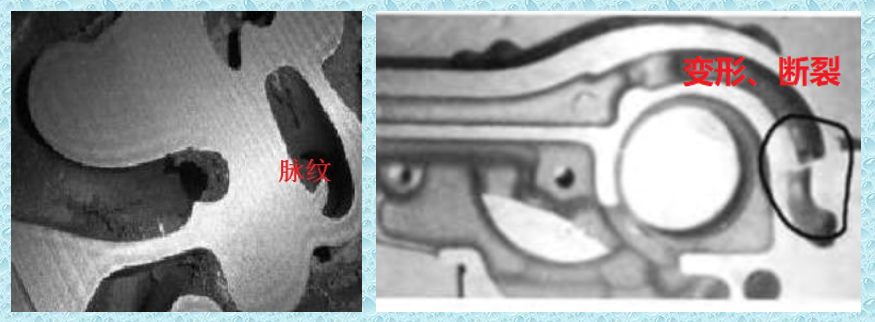
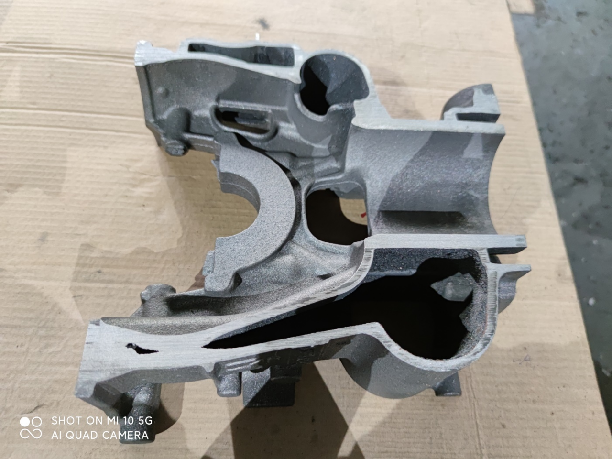
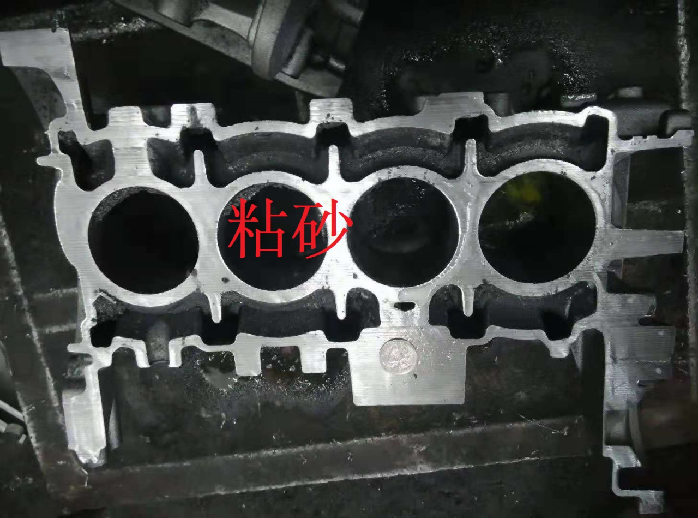
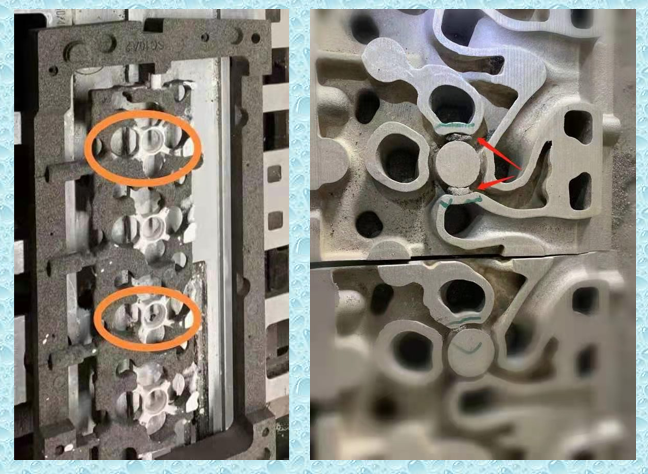
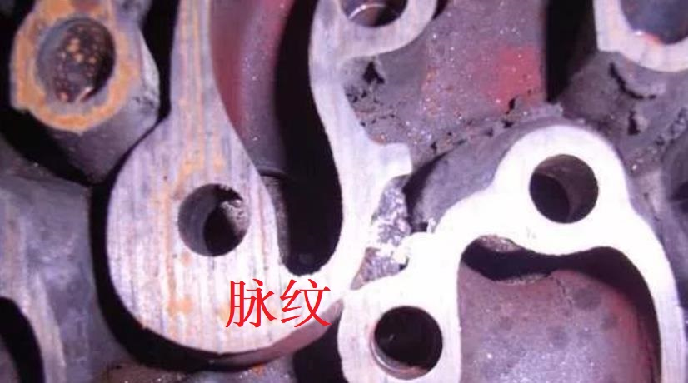
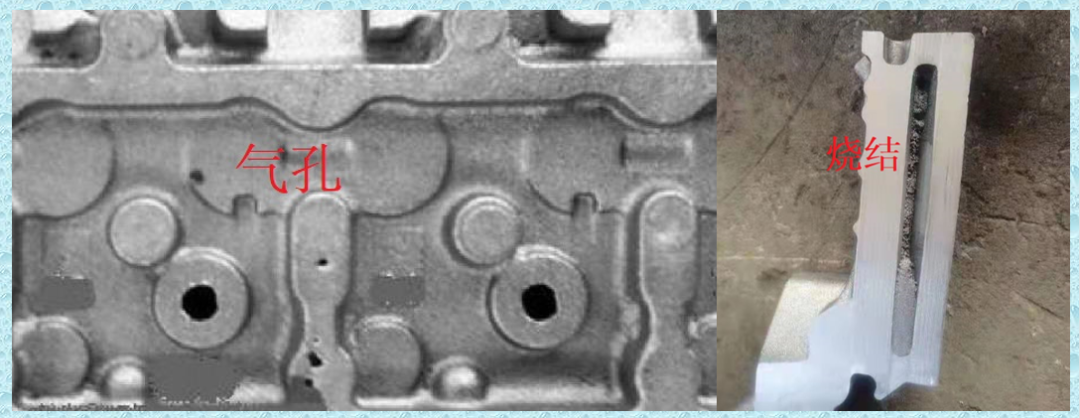
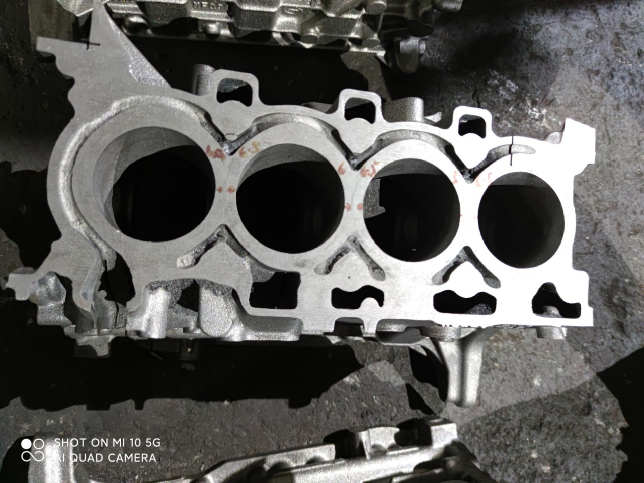
For at løse sådanne problemer, fra omkring 2010, begyndte nogle velkendte indenlandske motorstøbevirksomheder, såsom FAW, Weichai, Shangchai, Shanxi Xinke osv., at undersøge og teste anvendelsen af keramisk sand til fremstilling af cylinderblokke, topstykke vandkapper og oliepassager.Ens sandkerner eliminerer eller reducerer effektivt defekter såsom sintring af indre hulrum, sandklæbning, deformation af sandkerne og knækkede kerner.
Følg billeder er lavet af keramisk sand med cold box proces.
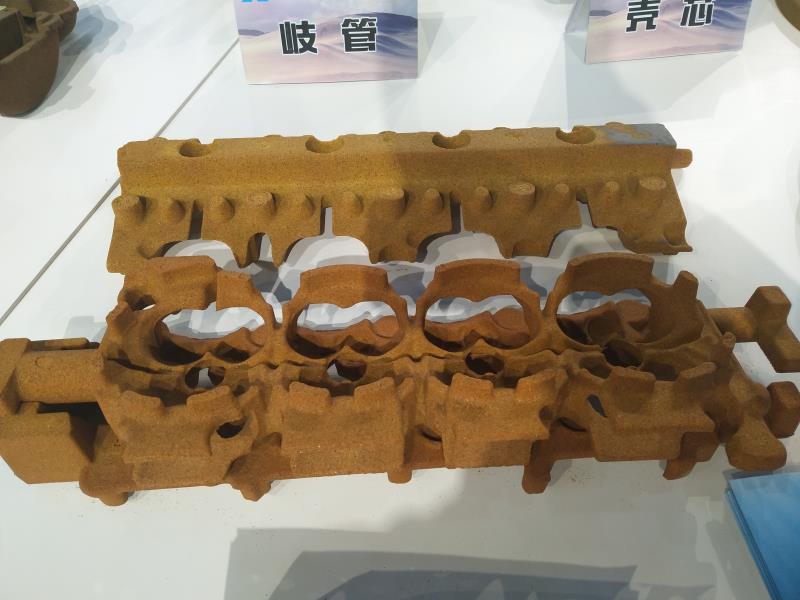
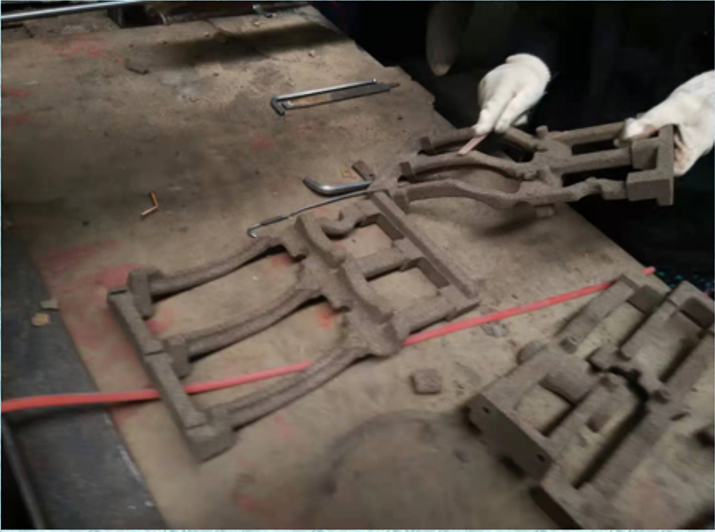
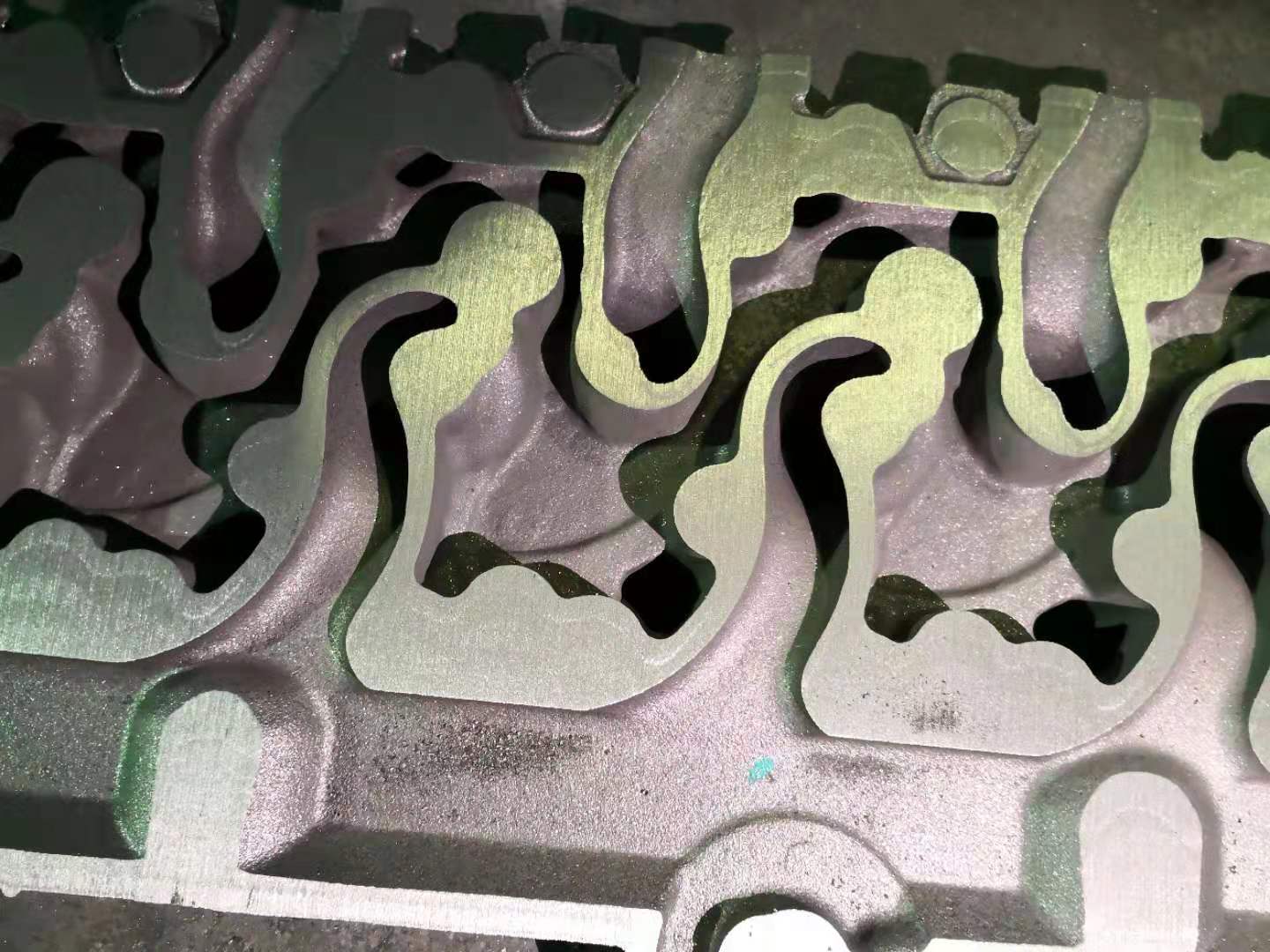
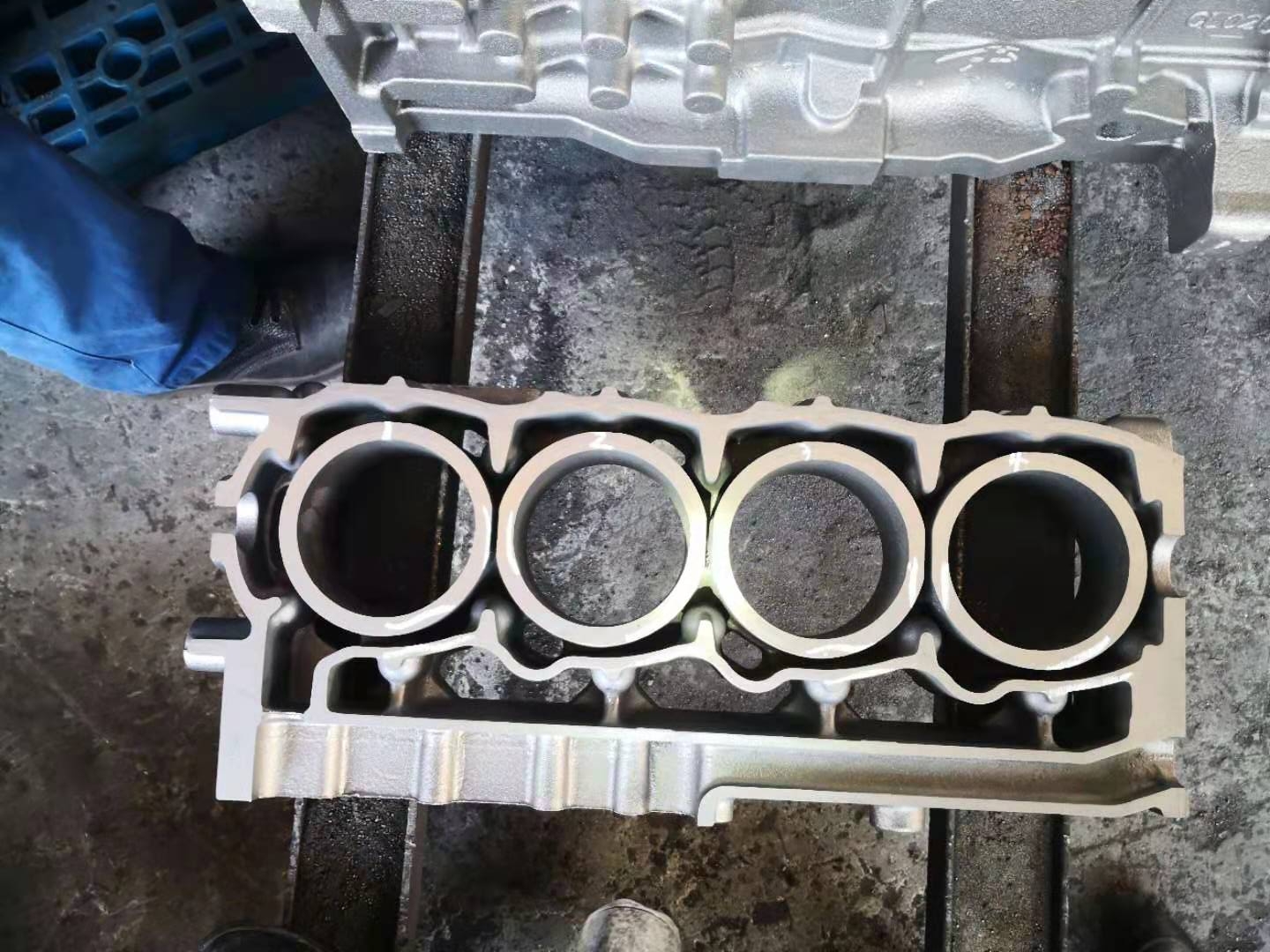
Siden da er keramisk sand blandet skuresand gradvist blevet fremmet i koldboks- og varmeboksprocesser og påført cylinderhovedvandkappekerner.Den har været i stabil produktion i mere end 6 år.Den nuværende brug af koldkassesandkernen er: i henhold til formen og størrelsen af sandkernen er mængden af tilsat keramisk sand 30%-50%, den samlede mængde tilsat harpiks er 1,2%-1,8%, og trækstyrke er 2,2-2,7 MPa.(Laboratorieprøvetestdata)
Resumé
Cylinderblok og hovedstøbejernsdele indeholder mange smalle indre hulrumsstrukturer, og hældetemperaturen er generelt mellem 1440-1500°C.Den tyndvæggede del af sandkernen sintres let under påvirkning af højtemperatursmeltet jern, såsom smeltet jern, der infiltrerer ind i sandkernen, eller producerer en grænsefladereaktion for at danne klæbrigt sand.Keramisk sands ildfasthed er større end 1800°C, i mellemtiden er den sande massefylde af keramisk sand relativt høj, den kinetiske energi af sandpartikler med samme diameter og hastighed er 1,28 gange større end silicasandpartikler, når der skydes sand, som kan øge tætheden af sandkerner.
Disse fordele er årsagerne til, at brugen af keramisk sand kan løse problemet med, at sand klæber i det indre hulrum af cylinderhovedstøbegods.
Vandkappen, indsugnings- og udstødningsdelene af cylinderblokken og topstykket har ofte åre-defekter.Et stort antal undersøgelser og støbepraksis har vist, at grundårsagen til åre-defekterne på støbeoverfladen er faseændringsudvidelsen af silicasand, som forårsager termisk spænding fører til revner på overfladen af sandkernen, hvilket forårsager smeltet jern at trænge ind i revnerne, er tendensen til vener større, især i koldboksprocessen.Faktisk er den termiske ekspansionshastighed for silicasand så høj som 1,5%, mens den termiske ekspansionshastighed for keramisk sand kun er 0,13% (opvarmet til 1000°C i 10 minutter).Muligheden for revnedannelse er meget lille, hvor på overfladen af sandkernen på grund af termisk ekspansionsspænding.Brugen af keramisk sand i sandkernen af cylinderblokken og topstykket er i øjeblikket en enkel og effektiv løsning på problemet med åredannelse.
Komplicerede, tyndvæggede, lange og smalle cylinderhovedvandkappe-sandkerner og cylinderoliekanalsandkerner kræver høj styrke (herunder højtemperaturstyrke) og sejhed og skal samtidig kontrollere gasdannelsen af kernesandet.Traditionelt bruges den belagte sandproces for det meste.Brugen af keramisk sand reducerer mængden af harpiks og opnår effekten af høj styrke og lav gasudvikling.På grund af den kontinuerlige forbedring af ydeevnen af harpiks og råsand har koldboksprocessen i stigende grad erstattet en del af den coatede sandproces i de seneste år, hvilket i høj grad forbedrer produktionseffektiviteten og forbedrer produktionsmiljøet.
2. Anvendelse af keramisk sand for at løse problemet med sandkernedeformation af udstødningsrøret
Udstødningsmanifolder arbejder under vekslende høje temperaturforhold i lang tid, og oxidationsmodstanden af materialer ved høje temperaturer påvirker direkte levetiden for udstødningsmanifolder.I de seneste år har landet løbende forbedret emissionsstandarderne for biludstødning, og anvendelsen af katalytisk teknologi og turboopladningsteknologi har øget arbejdstemperaturen for udstødningsmanifolden betydeligt og nået over 750 °C.Med den yderligere forbedring af motorens ydeevne vil arbejdstemperaturen på udstødningsmanifolden også stige.På nuværende tidspunkt anvendes generelt varmebestandigt støbestål, såsom ZG 40Cr22Ni10Si2 (JB/T 13044) osv., med en varmebestandig temperatur på 950°C-1100°C.
Det indvendige hulrum af udstødningsmanifolden skal generelt være frit for revner, kolde lukker, krympehulrum, slaggeindeslutninger osv., der påvirker ydeevnen, og ruheden af det indre hulrum kræves ikke at være større end Ra25.Samtidig er der strenge og klare regler om afvigelsen af rørets vægtykkelse.I lang tid har problemet med ujævn vægtykkelse og overdreven afvigelse af udstødningsmanifoldens rørvæg plaget mange udstødningsmanifoldstøberier.

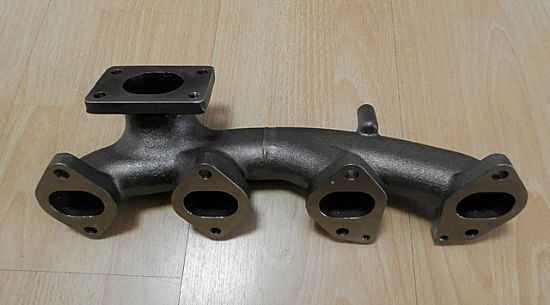
Et støberi brugte først silicasandbelagte sandkerner til at producere varmebestandige ståludstødningsmanifolder.På grund af den høje hældetemperatur (1470-1550°C) blev sandkernerne let deformeret, hvilket resulterede i fænomener uden for tolerance i rørets vægtykkelse.Selvom silicasandet er blevet behandlet med højtemperaturfaseændringer, på grund af forskellige faktorers indflydelse, kan det stadig ikke overvinde deformationen af sandkernen ved høj temperatur, hvilket resulterer i en bred vifte af udsving i tykkelsen af rørvæggen , og i alvorlige tilfælde vil det blive skrottet.For at forbedre styrken af sandkernen og kontrollere gasdannelsen af sandkernen, blev det besluttet at anvende keramisk sandbelagt sand.Når mængden af tilsat harpiks var 36 % lavere end mængden af silicasandbelagt sand, øgedes dens bøjningsstyrke ved stuetemperatur og termisk bøjningsstyrke med 51 %, 67 %, og mængden af gasdannelse er reduceret med 20 %, hvilket svarer til proceskrav om høj styrke og lav gasproduktion.
Fabrikken anvender silicasandbelagte sandkerner og keramiske sandbelagte sandkerner til samtidig støbning, efter rensning af støbegodset udfører de anatomiske inspektioner.
Hvis kernen er lavet af silicasandbelagt sand, har støbegodset ujævn vægtykkelse og tynd væg, og vægtykkelsen er 3,0-6,2 mm;når kernen er lavet af keramisk sandbelagt sand, er vægtykkelsen af støbningen ensartet, og vægtykkelsen er 4,4-4,6 mm.som følger billede
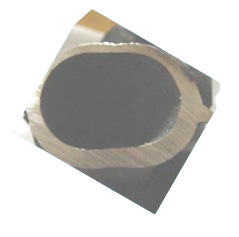
Silica sand belagt sand
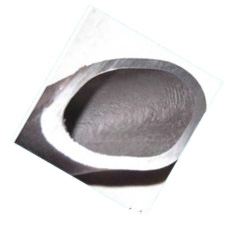
Keramisk sandbelagt sand
Keramisk sandbelagt sand bruges til at fremstille kerner, hvilket eliminerer brud på sandkernen, reducerer deformation af sandkernen, i høj grad forbedrer dimensionsnøjagtigheden af den indre hulrums strømningskanal i udstødningsmanifolden og reducerer sand, der klæber i det indre hulrum, hvilket forbedrer kvaliteten af støbegods og færdige produkter satsede og opnåede betydelige økonomiske fordele.
3. Påføring af keramisk sand i turboladerhus
Arbejdstemperaturen ved turbineenden af turboladerskallen overstiger generelt 600°C, og nogle når endda så højt som 950-1050°C.Skalmaterialet skal være modstandsdygtigt over for høje temperaturer og have god støbeevne.Skalstrukturen er mere kompakt, vægtykkelsen er tynd og ensartet, og det indre hulrum er rent osv., er ekstremt krævende.På nuværende tidspunkt er turboladerhuset generelt lavet af varmebestandigt stålstøbning (såsom 1.4837 og 1.4849 i den tyske standard DIN EN 10295), og der anvendes også varmebestandigt duktilt jern (såsom den tyske standard GGG SiMo, den amerikanske standard høj-nikkel austenitisk nodulært jern D5S osv.).
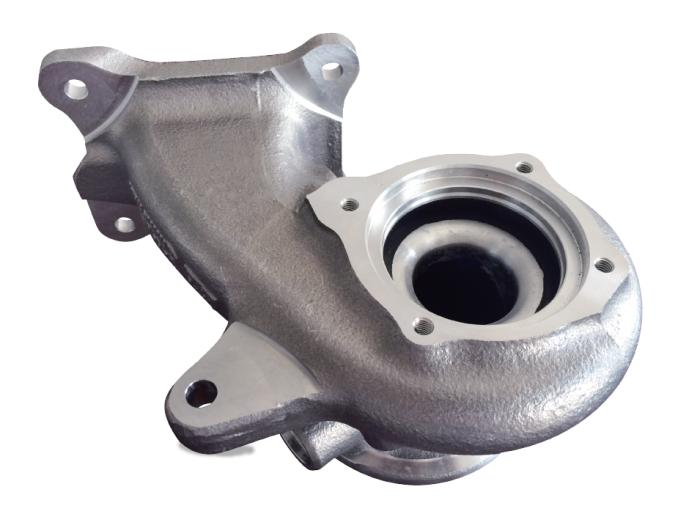
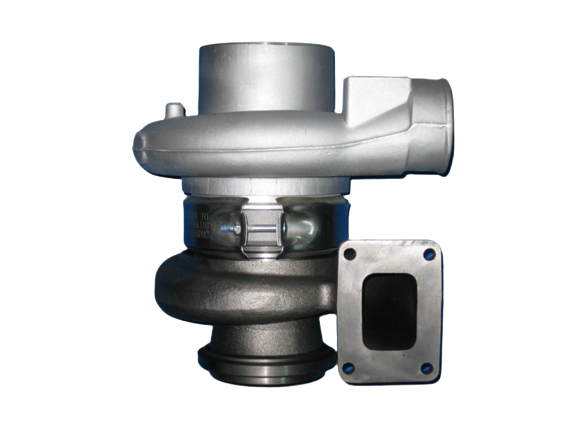
Et 1,8 T motor turboladerhus, materiale: 1,4837, nemlig GX40CrNiSi 25-12, hovedkemisk sammensætning (%): C: 0,3-0,5, Si: 1-2,5, Cr: 24-27, Mo: Max 0,5, Ni: 11 -14, hældetemperatur 1560 ℃.Legeringen har et højt smeltepunkt, en stor krympningshastighed, en stærk varm revne-tendens og høj støbebesvær.Den metallografiske struktur af støbegodset har strenge krav til restkarbider og ikke-metalliske indeslutninger, og der er også specifikke regler om støbefejl.For at sikre kvaliteten og produktionseffektiviteten af støbegods, vedtager støbeprocessen kernestøbning med filmbelagte sandskalkerne (og nogle koldboks- og varmebokskerner).I første omgang blev der brugt AFS50 skuresand, og derefter brugt ristet silicasand, men problemer som sandklæbning, grater, termiske revner og porer i det indre hulrum viste sig i varierende grad.
På grundlag af forskning og test besluttede fabrikken at bruge keramisk sand.Indledningsvis købt færdigbelagt sand (100% keramisk sand), og derefter indkøbt regenererings- og belægningsudstyr, og løbende optimeret processen under produktionsprocessen, brug keramisk sand og skrubsand til at blande råsand.På nuværende tidspunkt er det belagte sand groft implementeret i henhold til følgende tabel:
Keramisk sandbelagt sandproces til turboladerhus | ||||
Sand størrelse | Antallet af keramisk sand % | Harpiks tilsætning % | Bøjningsstyrke MPa | Gasudgang ml/g |
AFS50 | 30-50 | 1,6-1,9 | 6,5-8 | ≤12 |
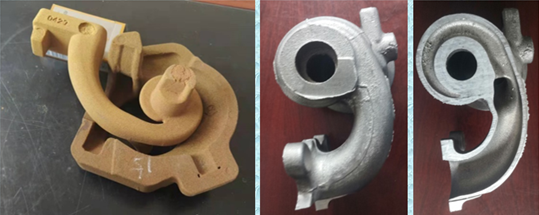
I løbet af de sidste par år har produktionsprocessen for dette anlæg kørt stabilt, kvaliteten af støbegods er god, og de økonomiske og miljømæssige fordele er bemærkelsesværdige.Opsummeringen er som følger:
en.Brug af keramisk sand, eller brug af en blanding af keramisk sand og silicasand til at fremstille kerner, eliminerer defekter såsom sandklæbning, sintring, åring og termisk revnedannelse af støbegods og realiserer stabil og effektiv produktion;
b.Kernestøbning, høj produktionseffektivitet, lavt sand-jern-forhold (generelt ikke mere end 2:1), mindre råsandforbrug og lavere omkostninger;
c.Kernehældning er befordrende for den overordnede genanvendelse og regenerering af affaldssand, og den termiske genvinding anvendes ensartet til regenerering.Ydeevnen for regenereret sand har nået niveauet for nyt sand til skuresand, hvilket har opnået effekten af at reducere indkøbsomkostningerne for råsand og reducere udledningen af fast affald;
d.Det er nødvendigt hyppigt at kontrollere indholdet af keramisk sand i regenereret sand for at bestemme mængden af tilsat nyt keramisk sand;
e.Keramisk sand har rund form, god fluiditet og stor specificitet.Når det blandes med silicasand, er det let at forårsage segregation.Om nødvendigt skal sandskydningsprocessen justeres;
f.Når du dækker filmen, prøv at bruge phenolharpiks af høj kvalitet og brug forskellige tilsætningsstoffer med forsigtighed.
4. Påføring af keramisk sand i motorens topstykke af aluminiumslegering
For at forbedre kraften i biler, reducere brændstofforbruget, reducere udstødningsforurening og beskytte miljøet, er lette biler udviklingstendensen i bilindustrien.På nuværende tidspunkt er støbegods til bilmotorer (inklusive dieselmotorer), såsom cylinderblokke og topstykker, generelt støbt med aluminiumslegeringer, og støbeprocessen af cylinderblokke og topstykker, når der bruges sandkerner, metalstøbning og lavtryksstøbning. støbning (LPDC) er de mest repræsentative.
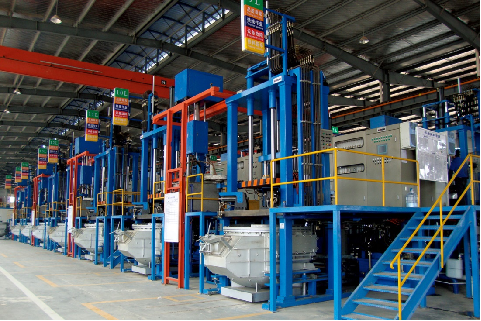
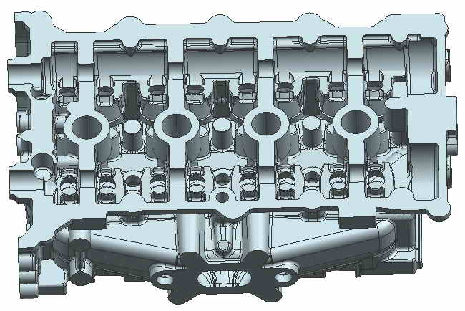
Sandkernen, det belagte sand og den kolde kasseproces af aluminiumslegering af cylinderblok og hovedstøbegods er mere almindelige, velegnede til højpræcision og storskala produktionskarakteristika.Metoden til at bruge keramisk sand ligner produktionen af støbejerns cylinderhoved.På grund af den lave hældetemperatur og lille vægtfylde af aluminiumslegering anvendes generelt lavstyrket kernesand, såsom en koldkassesandkerne på en fabrik, mængden af tilsat harpiks er 0,5-0,6%, og trækstyrken er 0,8-1,2 MPa.Kernesand er påkrævet Har god sammenklappelighed.Brugen af keramisk sand reducerer mængden af tilført harpiks og forbedrer i høj grad sammenbruddet af sandkernen.
I de senere år, for at forbedre produktionsmiljøet og forbedre kvaliteten af støbegods, er der flere og flere undersøgelser og anvendelser af uorganiske bindemidler (herunder modificeret vandglas, fosfatbindemidler osv.).Billedet nedenfor er støbestedet for en fabrik, der bruger keramisk sand uorganisk bindemiddelkerne sand aluminiumslegering topstykke.
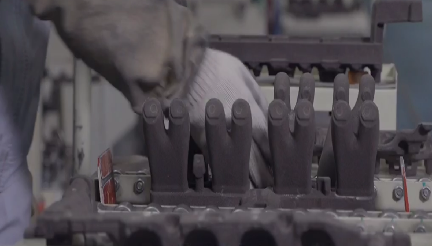
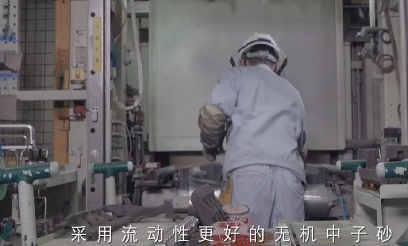
Fabrikken bruger keramisk sand uorganisk bindemiddel til at fremstille kernen, og mængden af tilsat bindemiddel er 1,8 ~ 2,2%.På grund af den gode fluiditet af keramisk sand er sandkernen tæt, overfladen er komplet og glat, og samtidig er mængden af gasproduktion lille, det forbedrer udbyttet af støbegods i høj grad, forbedrer sammenklappeligheden af kernesand , forbedrer produktionsmiljøet og bliver en model for grøn produktion.
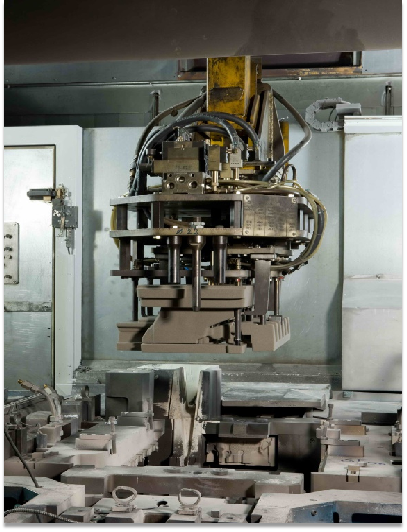
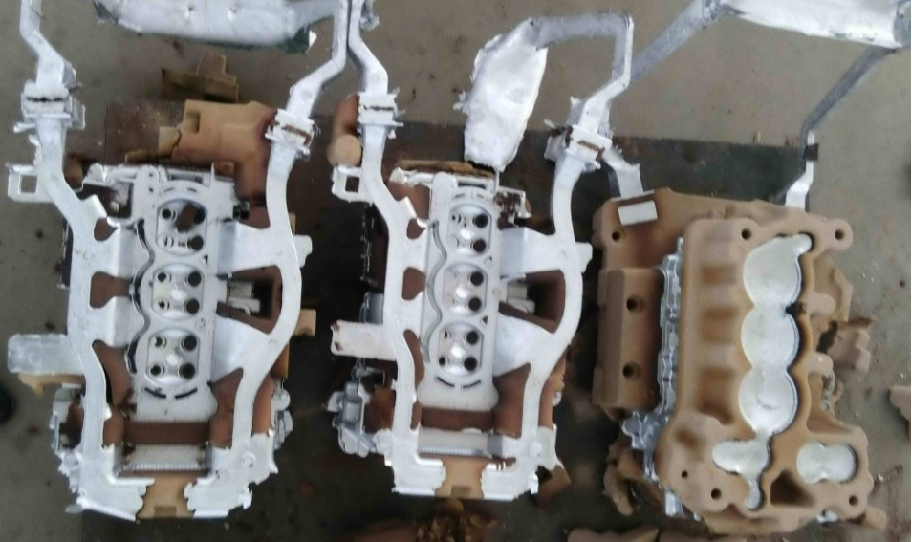
Anvendelsen af keramisk sand i motorstøbeindustrien har forbedret produktionseffektiviteten, forbedret arbejdsmiljøet, løst støbefejl og opnået betydelige økonomiske fordele og gode miljøfordele.
Motorstøberiindustrien bør fortsætte med at øge regenereringen af kernesand, yderligere forbedre brugseffektiviteten af keramisk sand og reducere emissioner af fast affald.
Fra perspektivet af brugseffekten og anvendelsesomfanget er keramisk sand i øjeblikket det støbespecielle sand med den bedste omfattende ydeevne og det største forbrug i motorstøbeindustrien.
Indlægstid: 27. marts 2023